![]() |
What is a grub screw?
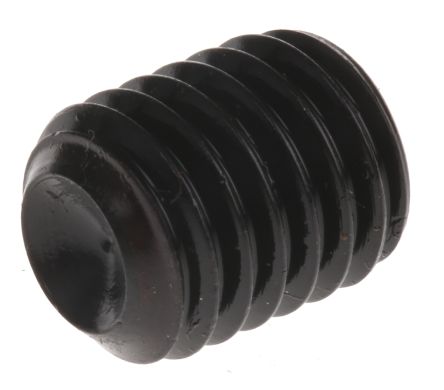
Grub screws, also known as set screws, are a type of fixing screw that’s most often used to join one component or part securely to another.
The design of grub screws means they’re intended to offer this secure gripping or joining facility without the use of a nut, as opposed to the typical arrangement found with most bolts. Despite this key difference, grub screws effectively function much the same as a bolt in practice. Because they’re fully threaded and designed to be driven into an existing tapped hole or socket - rather than driven into the surface, creating a new hole - they’re commonly considered a type of bolt, albeit with a few key differences.
The most obvious point of distinction between grub screws and other types of standard screws and bolts is that true grub screws tend not to feature a protruding head. Instead, they’re usually threaded right to the top, and are the same diameter all the way along their length, meaning that the grub screw can be fully driven into its hole to sit flush with (or even countersunk into, depending on the application) the workpiece.
Set screws often do feature a head - very likely a hex fitting - but without a threadless section immediately below it (again, this is different to the length of unthreaded shank you’d typically find on a standard bolt). Because they often feature no protruding screw head in the traditional sense, true grub screws tend to be driven by means of a sunken internal recess at what is still generally referred to as the ‘head end’.
The internal-wrenching drive used to seat a headless grub screw can be either a hex socket (as in Allen keys - you’ll need to know the correct allen key sizes for grub screws, which can usually be found on the packaging), a star (Torx) socket, a square socket (known as a Robertson drive), or a regular slotted drive. This will depend on the brand and model, and again on the exact type of screw being used for any given application.
What are grub screws used for
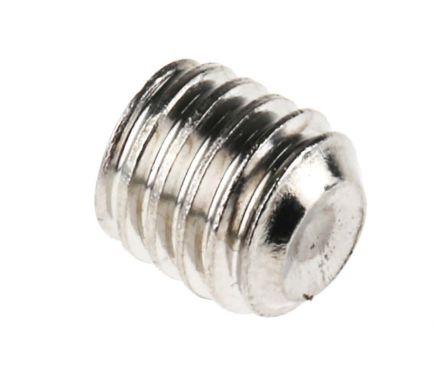
As stated in the section above, the most common uses for grub screws are to join or clamp one object or component tightly against another, but in specific scenarios where the use of a more traditional nut and bolt combination isn’t ideal for various reasons.
Grub screws can often prove especially useful in situations where a standard nut and bolt would impede the optimal functioning of an object or component(s), or else would not achieve the clean aesthetic the installer is aiming for on the visible/external faces of an item. They’re almost always found being used in mechanical systems where two or more metal surfaces rub or press directly together, and where there isn’t room to fit a bolt or other type of protruding head between the two flush surfaces without limiting proper functionality or movement of the part(s).
A grub set screw is slightly more versatile than a traditional bolt in this sense, due to its ability to be driven flush with surfaces or recessed and effectively hidden from view. The end result is a very unobtrusive fixing that can be tucked out of sight more easily than a traditional bolt with a locking nut.
Typical examples of uses for grub screws might include any situation where one object or component needs to clamp to another tightly via friction, but where protruding parts of the fastener would interfere with smooth functioning of the items in question. Grub screws for this purpose are especially widely used in architectural ironmongery, and are a very common feature found wherever door handles are attached to spindle shafts.
Another common usage scenario involving grub screws or set screws is when attaching a pulley hub to a shaft - in this case, the end-point of the set screw pushes firmly against the shaft, possibly with some degree of elastic or plastic deformation of the part(s) at the point of contact, to provide increased grip. The fastening action is therefore achieved through friction between grub screw and shaft.
Besides aesthetics, another advantage of using grub screws (with no leading or trailing edge exposed at the head end) is that they can often offer better resistance to weathering and corrosion as a result. They can also be driven with considerably more torque force than traditional screws, as the uniform diameter right the way along the full length of the grub screw shaft means that they don’t begin to split the hole apart as they go in further. Instead, the the surrounding material into which the set or grub screw is driven will work to reinforce the fastening as it goes in.
One potential downside of flush-set grub screws, however, is that they can be quite difficult to remove once driven with full force to sit flush with or countersunk into the surface of the workpiece, especially if they do become corroded or the drive slot is damaged due to excessive torque going in. In these sorts of scenarios, grub screws might often need to be drilled out for proper removal, which can be challenging in itself due to the high tensile strengths of materials generally used to manufacture grub and set screws.
How to use set screws
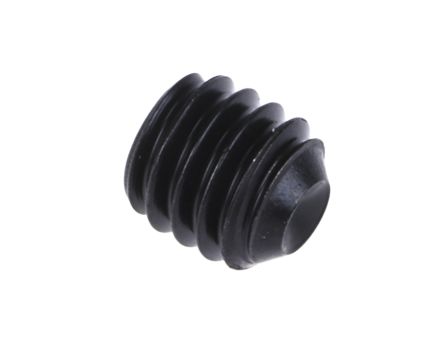
As well as in architectural ironmongery, grub screws are often used in a wide range of industries and sectors to secure all manner of collets, gears and handles to their respective mounting brackets or hardware.
You’ll nearly always need a hex drive or Allen wrench attachment to use flush-seated headless grub screws. Although slotted varieties are sold for use with standard flat-head screwdrivers, they’re less common than hex, Torx or Allen internal-wrenching drives, because slotted varieties are inherently less robust and more easily deformed during insertion under high torque forces.
How to remove a stuck grub screw
As noted above, the process for removing a stuck or bound grub set screw can be challenging - not necessarily more so than standard screws by design, but the fact is that grub screws are very often driven with far higher torque in order to achieve their intended friction-based clamping or binding function. This can make backing them out again tricky under some circumstances.
Because grub screws very often feature a recessed hole or slot at one end for a hex drive, Allen wrench or flat-head screwdriver - as opposed to a traditional head - they can be awkward to get sufficient purchase on for easy removal. This is especially the case if the drive recess has been damaged during insertion, or where corrosion has occurred around the threads.
However, the basic steps to removing a grub screw will be largely similar to those required for removing any other type of threaded fastener:
-
You can apply a penetrating lubricant to help reduce and remove any rust or corrosion present around the threads of the grub screw prior to starting
-
Insert the correct kind of drive for the type of grub screw in question, and make sure it is securely seated
-
If the screw won’t immediately back out with a counterclockwise torque force, you can attempt to turn the grub screw slightly further right (clockwise), in the direction you’d use to tighten it more - this can often break a rust seal more easily than trying to go directly to backing it out
-
If it won’t budge and needs to be drilled out, start by taking an awl or centre punch and using it with a hammer to make a small indentation in the visible end of the grub screw - this will help reduce the risk of the drill bit from slipping or wandering while you drill through the metal
-
Choose a suitable diameter drill bit for drilling out the stuck grub screw in question (this will often be specified for different gauges of screw on many screw extractor and drill bit sets)
-
Once you’ve drilled the hole, insert the most suitable size of screw extractor into the hole you’ve just made, tap it in with a hammer to ensure a secure fit, then proceed as normal to attempt to turn the extractor counterclockwise using the added torque from a tap-and-die kit handle or similar
Different types of grub screw
When buying grub screws or set screws from most manufacturers and suppliers to the UK market, you'll usually find up to six different variants of grub screw shapes on offer. These include:
-
flat-end grub screws, in which the end opposite the head makes a simple flush contact between the parts being joined
-
domed point end grub screws, which offer a slightly pointed or tapered tip that provides more pressure at the point of contact (due in part to encouraging a small degree of elastic deformation, as well as the more concentrated pressure zone)
-
cone point tip grub screws, which are ideal for exerting additional force when joining items made from softer materials, or to fit into an existing depression in the piece being mated to
-
cup point grub screws, which offer much the same function as cone point varieties but can be driven still further to provide even more torque and gripping force
-
knurled point grub screws, which do much the same as cup point versions but also feature a serrated end for additional friction/grip
-
dog point grub screws, which have a slightly narrower diameter shaft protruding from the grub screw opposite the head end - this functions as a sort of spindle or pivot, similar to those found on certain rivets, and can be used to insert into or support other components/pieces of equipment that are required to rotate around it
Hex grub screws
Hex heads are by far the most common type of drive style from both grub and set screws, whether it’s an internal recessed drive socket (as in a true grub screw) or a protruding head on a set screw (more similar to a familiar standard bolt, but with full threading of the shaft). Hex grub screws provide a very secure, non-slip and deformation-resistant drive socket for seating grub and set screws with high torque forces.Nylon grub screws
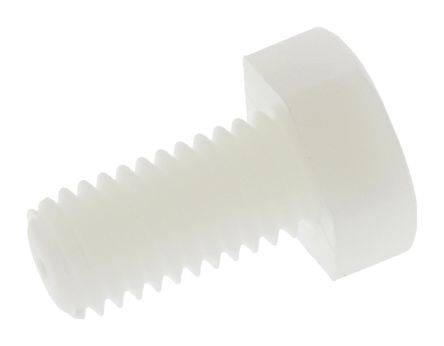
Nylon or nylon-tipped grub screws and set screws tend to be preferred in applications where a tight and secure friction-based fixing is required, but where it’s important for aesthetic or structural reasons not to mark or damage the mating surface.
They offer an additional degree of plastic deformation on tightening under high torque, which helps them fit to the exact contours of the component or object being mated to, providing tighter grip (especially on uneven or rough surfaces). Again, various formats of nylon hex head set screws are widely available from most suppliers and wholesalers in the UK.
Brass grub screws
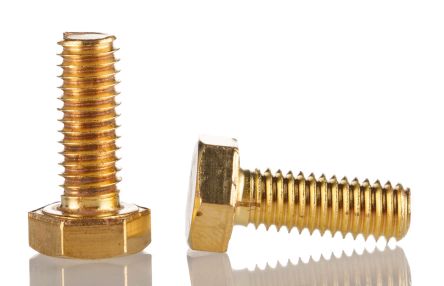
Brass grub screws are a common material chosen for many domestic, professional and hobbyist applications, Brass grub screws for door handles are notably popular choices when it comes to securing internal ironmongery and smaller fittings. Brass is prized as a material in applications where low friction between moving parts is required (such as locks, door handles, gears and bearings), many of which are jobs commonly associated with grub and set screws as we’ve already seen.
Brass is an alloy of copper and zinc, and the relative proportions of metals in the alloy can vary according to manufacturer specifications and the required mechanical functioning of the screws. It’s non-sparking, and widely used is used for applications requiring some degree of decorative or aesthetic attention thanks to its gold-like appearance. Brass grub screws are very widely available from most suppliers in the UK.
Grub screw sizes
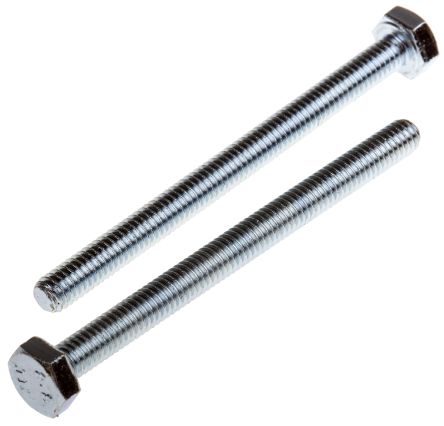
Regardless of the exact type or shape of grub screws and set screws you’re looking to buy, you’ll generally find them sold to a range of sizing specifications, including grub screw sets defined in both imperial (inches and fractions of inches) and metric (millimetres) units of measurement.
Very often you will be able to access a set screw sizing chart, in order to compare and contrast between the two to determine the ideal set screw size for the task you need them to perform.
Because they’re often chosen to work in tight or confined spaces, or as part of more intricate assemblies, it’s common to find grub screws available in a wide range of very small sizes. These can start from as little as a couple of millimetres in standard hardware configurations, but anything under about 4mm would typically be considered a ‘small’ grub or set screw. Above this, they can come in just as wide a range of sizes as most other screw types.
As a buyer, it’s important to know which stated measurement on the package refers to which dimensions of the screw. In most cases with UK suppliers, you’ll generally see sizings given in the format akin to ‘M8 x 12mm’ or an equivalent variant with different numbers.
The ‘M’ here basically signifies metric units - an M8 x 12mm grub screw will be 8mm wide at the major (outer) diameter of the thread, and 12mm long. Similarly, an M5 x 150mm set screw will be 5mm in diameter across its threaded section, and 150mm long from head to end.
Common ‘M’ sizes for grub and set screws include:
M1 Grub and Set Screws | M4 Grub and Set Screws | M8 Grub and Set Screws | M14 Grub and Set Screws |
---|---|---|---|
M2 Grub and Set Screws |
M5 Grub and Set Screws |
M10 Grub and Set Screws |
M16 Grub and Set Screws |
M3 Grub and Set Screws |
M6 Grub and Set Screws |
M12 Grub and Set Screws |
M20 Grub and Set Screws |
Product spotlights
Use one of these links to view the products on the RS website