- Published Oct 29, 2024
- Last Modified Oct 29, 2024
- 13 min
Understanding Epoxy Resin and Its Uses

Reviewed by Stephen Bettles, Technical Support Engineer
Epoxy resin is a highly versatile adhesive widely utilized in construction, woodworking, and manufacturing due to its exceptional bonding strength and durability. Known for its resistance to chemicals and moisture, epoxy resin is ideal for a variety of applications, ranging from creating waterproof barriers to providing heat resistance in demanding environments.
This guide thoroughly examines the different types of epoxy resin, their specific uses, and the benefits they offer. It also addresses essential safety precautions necessary when handling these materials to mitigate potential hazards. Whether you are a DIY enthusiast or a professional craftsman, this guide will equip you with the knowledge needed to maximize the advantages of epoxy resin in your projects.
What is Epoxy Resin?
Epoxy resin, also known as polyepoxide, is a flexible material used in many industries because of its strong adhesive abilities and toughness. It comes as a two-part system, a resin and a hardener, that are mixed in specific amounts, usually between 2:1 and 4:1. One of the key features of epoxy resin is its strong flexibility, making it suitable for both home and commercial applications.
Epoxy resins are favored for their long pot life, allowing users ample time to work with the material before it begins to cure. Fast-setting varieties provide approximately 15 minutes of working time, while regular or slow-setting options can extend this period to around 100 minutes. This flexibility makes epoxy resin ideal for a wide range of projects, from intricate crafts to large-scale industrial applications.
The positive attributes of epoxy resin include its toughness, strong adhesion to various substrates (such as wood, metal, glass, and concrete), and excellent chemical resistance. These qualities make it a preferred choice in multiple sectors, including construction, manufacturing, and electronics. In the construction industry, epoxy resin is commonly used for bonding materials and repairing structures. In manufacturing, it plays a crucial role in producing electronic components like fiber optics and circuit boards.
Essential Safety Tips for Using Epoxy Resin
When working with epoxy resin, it is essential to follow specific safety precautions to protect yourself from potential hazards associated with this versatile material. Here are some crucial safety tips to ensure a safe and enjoyable experience while using epoxy resin.
1. Wear Appropriate Personal Protective Equipment (PPE)
To safeguard your hands from exposure to epoxy resin and hardeners, always wear nitrile gloves. These gloves are preferred because they offer excellent chemical resistance and are less likely to react with the resin. If resin accidentally contacts your skin, use baby wipes for initial cleanup, then wash the area thoroughly with soap and water. For stubborn residue, an exfoliant can be particularly effective in removing any lingering traces.
In addition to gloves, it is advisable to wear a plastic apron to protect your clothing and skin from spills. Safety goggles are also essential for eye protection; if any resin splashes into your eyes, flush them with water for at least 15 minutes and seek medical attention immediately.
2. Ensure Proper Ventilation
Working with epoxy resin can produce harmful fumes that may irritate your respiratory system. To minimize exposure, ensure that your workspace is well-ventilated by opening windows or using fans to promote airflow. If adequate ventilation cannot be achieved, consider wearing a respirator mask designed to filter out organic vapors and protect your lungs from harmful inhalants.
3. Maintain a Clean and Organized Workspace
A clean workspace is crucial for preventing accidental exposure to epoxy resin. Keep your work area tidy and free of clutter. Ensure that children and pets are kept away from the workspace to avoid any accidental contact with the resin. Additionally, refrain from eating or drinking in the work area to prevent accidental ingestion of resin particles.
4. Proper Cleanup and Disposal Procedures
After completing your project, clean all tools and surfaces immediately using appropriate solvents like isopropyl alcohol or acetone for uncured resin. Cured epoxy can be more challenging to remove; use paint thinner or adhesive removers if necessary. Dispose of any leftover resin responsibly by following the manufacturer's guidelines, never pour it down the drain or throw it in regular trash as this can harm the environment.
Types of Epoxy Resin
Epoxy resin can be categorized into two primary types: glycidyl and non-glycidyl epoxy resins. Understanding the different types of epoxy resin is essential for selecting the right one for your project.
Glycidyl Epoxy Resins
Glycidyl epoxy resins are further divided into several subcategories, including glycidyl-ether, glycidyl-ester, and glycidyl-amine. Among these, glycidyl-ether epoxies are the most commonly used, particularly those derived from bisphenol-A and novolac formulations.
1. Bisphenol Epoxy Resins
The most widely utilized commercial epoxy resin is Bisphenol-A diglycidyl ether (DGEBA). This resin is created through the reaction of bisphenol-A with epichlorohydrin in the presence of a basic catalyst. DGEBA is known for its low molecular weight, making it suitable for various applications requiring strong adhesion and durability.
2. Novolac Epoxy Resins
Novolac epoxy resins are produced by reacting phenol and formaldehyde, followed by a reaction with epichlorohydrin. These resins, such as epoxyphenol novolac (EPN) and epoxycresol novolac (ECN), do not contain solvents or volatile organic compounds (VOCs), making them safer to use without requiring respirators. They offer high adhesive strength and excellent durability, making them ideal for demanding applications.
Non-Glycidyl Epoxy Resins
Non-glycidyl epoxy resins can be classified as either aliphatic or cycloaliphatic.
1. Aliphatic Epoxy Resins
These resins are produced through processes such as double bond epoxidation or reactions with epichlorohydrin. Cycloaliphatic epoxides contain one or more aliphatic rings in their structure, providing them with unique properties such as low viscosity, excellent weather resistance, and high glass transition temperatures (Tg). They are often used in applications requiring transparency and UV resistance.
2. Halogenated Epoxy Resins
Halogenated epoxy resins incorporate brominated or fluorinated compounds to enhance specific properties like flame resistance. While brominated bisphenol A is commonly used in electrical applications for its flame-retardant qualities, the production of these resins is limited due to higher costs and lower glass transition temperatures.
Specialty Epoxy Resins
In addition to the standard types, there are specialty epoxy resins designed for specific applications:
1. Epoxy Resin Diluents
These are created by glycidylating aliphatic alcohols or polyols and can be monofunctional, difunctional, or higher functionality compounds. They help reduce viscosity and improve processing characteristics.
2. Glycidylamine Epoxy Resins
Formed from aromatic amines reacting with epichlorohydrin, these resins have high functionality levels and include industrial grades like triglycidyl-p-aminophenol. They typically exhibit low to medium viscosity at room temperature, facilitating easier processing compared to other types.
Epoxy Putty
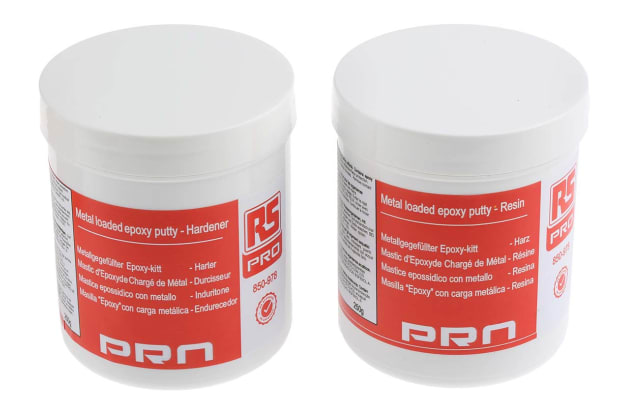
Epoxy putty refers to a range of room-temperature curing substances that function as effective space-filling adhesives. These products are designed to provide strong adhesion and sealing properties, making them ideal for various applications across multiple industries. The composition of epoxy putty can vary significantly depending on the manufacturer and intended use, but they all share the common ability to bind, set, and waterproof a wide array of materials.
One of the key advantages of epoxy putty is its waterproof sealing capabilities, which ensure that once applied, it protects against moisture intrusion. This feature is particularly beneficial in construction and repair tasks where water exposure is a concern.
Curing Time and Process for Epoxy Resin
Uncured epoxy resins typically exhibit poor mechanical, chemical, and heat resistance properties. However, these characteristics can be significantly enhanced through a process known as curing. Curing involves a chemical reaction between the resin and suitable curatives or hardeners, leading to the formation of durable cross-linked thermoset structures.
The curing time for different epoxy pastes and putties can vary widely. For critical projects, it is generally recommended to cure the epoxy under warm conditions for an extended period. Allowing up to 72 hours for the setup of epoxy ensures the formation of strong adhesive bonds. Full curing time is especially crucial for applications that will experience high pressure or stress.
Curing can occur through two main mechanisms: homopolymerization, where the resin reacts with itself, or copolymerization, which involves polyfunctional curatives or hardeners. Various hardeners are available, including amines, acids, acid anhydrides, phenols, alcohols, and thiols. The reactivity levels of these hardeners vary significantly; for example, phenols have lower reactivity compared to aliphatic amines.
To accelerate the curing process, small amounts of accelerators such as tertiary amines or carboxylic acids can be added.
Epoxy Resin Uses and Application Methods
Epoxy resin has a wide range of applications across multiple sectors, including coating, adhesion, and the creation of composite materials reinforced with carbon fiber or fiberglass. Its properties can also be modified for specific needs; for instance, silver-filled epoxies offer high electrical conductivity.
Here are some notable epoxy adhesive products:
Araldite Rapid Epoxy Adhesive
Material Compatibility: Ceramics, wood, chipboard, glass, metal, most hard plastics
Epoxy Color: Clear
Araldite Fusion Epoxy Adhesive
Material Compatibility: Ceramics, wood, glass, metal, hard plastics, stone, marble, leather, porcelain, brick, concrete
Epoxy Color: Transparent
Scotch-Weld Epoxy Adhesive
Material Compatibility: Plastics, composites, metal
Epoxy Color: Various options available
Loctite Hysol Epoxy Adhesive
Material Compatibility: Ceramics, metal, plastics
Epoxy Color: Various options available
Epoxy Resin Adhesives
Epoxy resin adhesives are categorized as structural or engineering adhesives and include chemical varieties such as polyurethane and cyanoacrylate. They are widely used in industries for bonding components in aircraft parts, golf clubs, skis, and snowboards. These adhesives provide strong adhesion to materials like wood, metal, glass, and stone; however, their effectiveness diminishes at temperatures exceeding 350°F (177°C).
Industrial Applications of Epoxy Resin
In industrial settings, epoxy resin is utilized for creating molds, master models, laminates, castings, and fixtures. This plastic tooling serves as an excellent alternative to traditional materials like metal and wood by enhancing efficiency while reducing costs and lead times in various manufacturing processes.
In the electrical industry, epoxy resin plays a crucial role in constructing motors, generators, transformers, insulators, and printed wiring boards (PWBs). Its high electrical insulation properties protect components from short-circuiting caused by dust and moisture accumulation.
Consumer Applications of Epoxy Resin
Due to its exceptional adhesive qualities, epoxy resin is popular among consumers for repairing domestic items. It allows for quick fixes on fragile materials such as glass and ceramics while also being effective on wood and metal repairs.
Artistic Uses of Epoxy Resin
Artists frequently use epoxy resin combined with pigments for creative applications. It can be layered to create stunning visual effects in artwork or used in jewelry making and decoupage projects.
Epoxy Coatings and Painting
Epoxy paint, often referred to as epoxy floor coating, is a popular choice for covering surfaces in garages, basements, and patios. This type of paint is formulated by combining acrylic paint with a one-part epoxy resin, resulting in a durable finish that is both attractive and functional. Users can achieve various color options by applying acrylic epoxy paint, which dries similarly to traditional paint. Available colors range from metallic blue to cream, allowing for customization that enhances the aesthetic appeal of any space.
The formulation of epoxy coatings consists of a compound made from epoxy resin and a polyamine hardener. When these components are mixed, they undergo a chemical reaction that creates cross-linked structures during the curing process. This unique property of epoxy coatings provides exceptional protection against abrasion, corrosive substances, and extreme temperatures, making them ideal for high-traffic areas.
Benefits of Epoxy Coating
Epoxy coatings offer numerous advantages that make them an excellent choice for both residential and commercial applications:
- Durability: Epoxy coatings are known for their long-lasting nature. They can withstand heavy foot traffic and resist wear and tear from daily use.
- Non-Toxicity: Many epoxy coatings are formulated to be low in volatile organic compounds (VOCs), making them safer for indoor environments.
- Weather Resistance: Epoxy coatings are highly resistant to moisture, UV rays, and harsh weather conditions, ensuring they maintain their integrity over time.
- Impact Resistance: The tough surface of epoxy coatings can absorb shocks and impacts, preventing damage from dropped tools or heavy equipment.
- Chemical Resistance: Epoxy coatings provide a robust barrier against various chemicals, oils, and solvents, making them suitable for garages and industrial settings.
- Ease of Maintenance: Surfaces coated with epoxy are easy to clean and maintain. Their smooth finish prevents dirt accumulation and allows for simple sweeping or mopping.
FAQs
Related links
- A Complete Guide to Epoxy Resin
- Ball Bearings - A Complete Buying Guide
- Comprehensive Guide to PTFE Tape and Its Applications
- Complete Guide to Travel Plug Adapters
- Understanding PID Temperature Controllers and Their Uses
- A Complete Guide to Gate Valves
- Everything You Need to Know About Hacksaws
- A Complete Guide to Spur Gears