- Published Mar 15, 2024
- Last Modified Mar 15, 2024
- 6 min
How to Handle & Prevent Electric Motor Overheating
Learn how to prevent your electric motor from overheating. Identify the common causes of your motor overheating and how to solve or prevent it.

Overheating in electric motors is not just a common issue; it's a critical one that can cause premature failure, significant downtime, and increased operational costs. This makes it essential for business owners in the Philippines to be vigilant with their electric motors, especially ones in manufacturing and construction sites where they are commonly used.
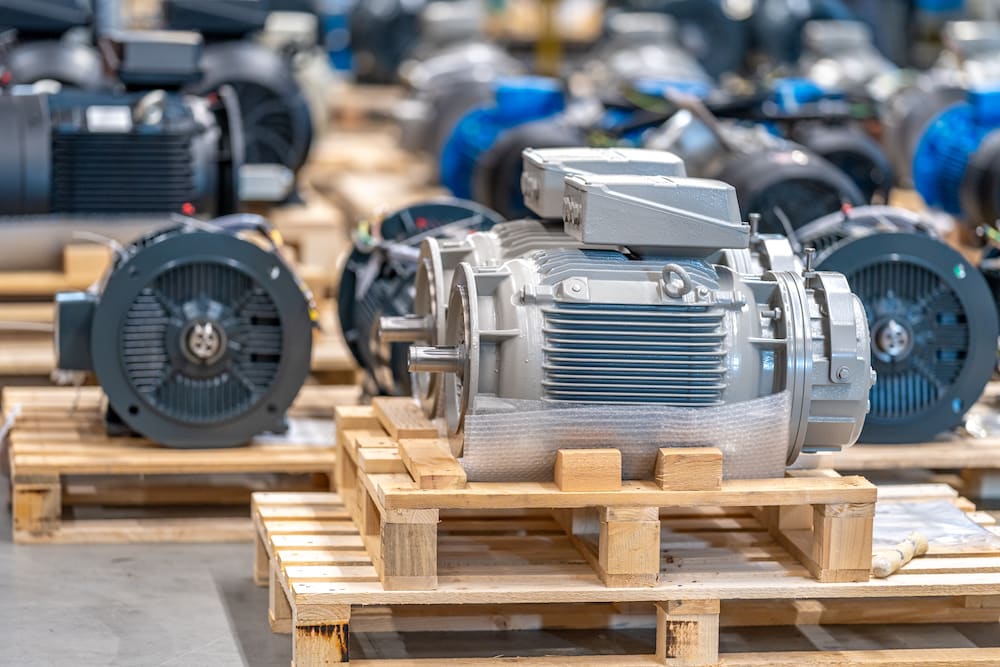
What Are the Common Causes of Electric Motor Overheating?
Many factors contribute to your electric motor overheating and some of them include:
1. Overload
An overload occurs when a motor is required to handle a load beyond its design capacity. This not only reduces efficiency but also increases the motor's operating temperature. Most motors run efficiently when they only need to manage 75% of their load rating. This enables the motor to run at a lower temperature and consume less power.
2. Ventilation Issues
Most equipment with motors is designed to have a system that helps offload heat produced during operation. However, some factors can interrupt this system and its function, such as clogged air ducts or a buildup of contaminants. Moreover, external factors can also contribute to an overheating motor, like the temperatures brought about by humid weather conditions. The hot weathers in the Philippines exacerbates these challenges, especially during the summer months, March to May, when temperatures may be high.
3. Voltage Irregularities
Generally, motors operate most efficiently when the voltage supplied matches the voltage rating specified by the manufacturer on the nameplate. Operating a motor with less voltage than recommended necessitates a greater current to generate the required power, leading to increased heat from resistance. Similarly, supplying a voltage higher than the motor's saturation point also increases current and, consequently, additional heat. An imbalance in voltage in a 3-phase motor causes overheating due to voltage spikes.
4. Eddy Currents
If your application uses an AC motor, know that this type of electric motor is made of many pieces of laminated steel, and the windings are wound through its core. As such, the changing magnetic fields from the spinning rotor can cause a phenomenon known as Eddy Currents within the steel core. When your AC motor has Eddy Currents, it reduces energy from the steel core and exhibits heat.
5. Current Density
When the diameter of your motor winding wire decreases, your electrical resistance increases. An increase in electrical resistance leads to a higher energy loss in the form of heat. This is because as the electrons encounter more resistance, more energy is converted into heat instead of being used for productive work by the motor.
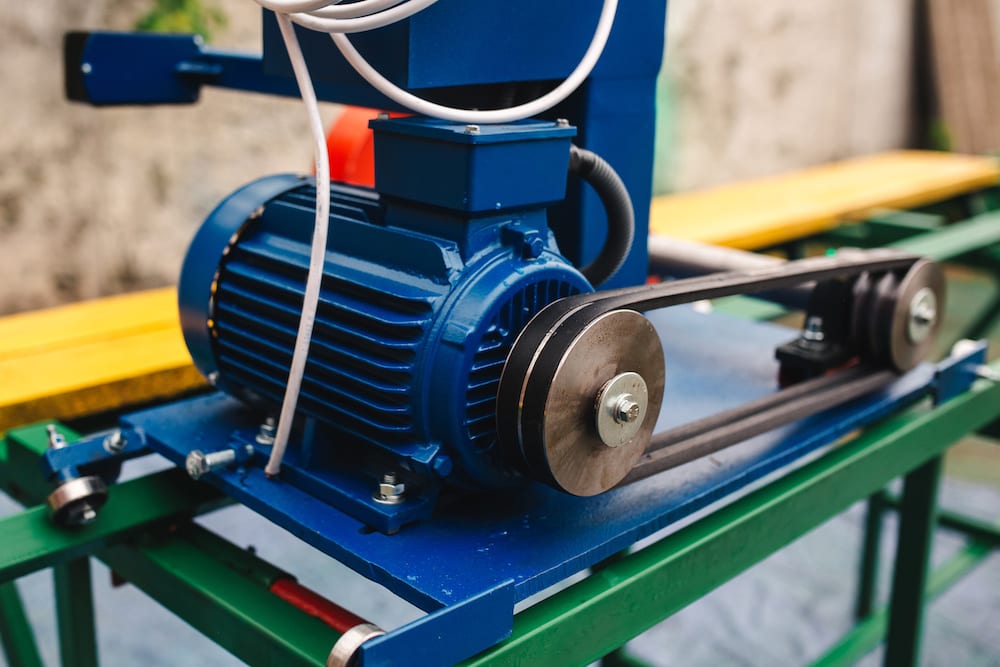
How to Prevent & Manage Overheating Electric Motors
Here are detailed solutions to preventing and handling overheating in electric motors:
1. Addressing Overload Conditions
Preventing overload conditions is paramount in avoiding motor overheating. This can be done by closely monitoring and adjusting the loads applied to motors by utilizing smart sensors and control systems. These technologies enable real-time adjustments and load distribution, ensuring the motor operates within its capacity, thereby maintaining optimal performance and preventing overheating.
2. Improving Ventilation
The efficiency of the motor's cooling system is directly tied to its ventilation. As such, regular maintenance to ensure the cooling system is functioning properly is essential. This includes cleaning vents and making sure there is unobstructed airflow around the motor. Moreover, environmental adjustments, such as removing nearby heat sources and ensuring the motor is not enclosed in a tight space without adequate air circulation, can also help maintain an optimal cooling environment.
3. Maintaining Proper Voltage
Maintaining the voltage levels within the manufacturer's recommended ranges is critical to avoid overheating. Implementing solutions to correct voltage imbalance and mitigate the effects of harmonics can have a significant positive impact on the motor's temperature regulation. Techniques may include using voltage regulators, phase converters for three-phase motors, or harmonic filters to ensure voltage stability and reduce the risk of overheating.
4. Mitigating Eddy Currents
Design considerations must be made to mitigate Eddy currents and ensure motor efficiency. Effective mitigation strategies involve careful design considerations, such as the use of laminated magnetic cores. These cores are constructed from thin layers of magnetic material, each insulated from the others, which helps to reduce the pathways available for Eddy currents to flow, thereby minimizing their formation.
Additionally, selecting appropriate materials that have lower electrical conductivity for parts of the motor where Eddy currents are likely to occur can further reduce losses. Optimizing the overall design of the motor, including its geometry and the arrangement of its components, also plays a critical role in reducing the impact of Eddy currents. By implementing these strategies, manufacturers can significantly improve electric motor efficiency, leading to lower operational costs and enhanced performance.
5. Optimizing Current Density
Choosing the correct wire size and type of insulation is crucial for balancing the motor's efficiency and temperature control. A proper understanding of the relationship between electrical resistance and heat generation can guide in selecting the right materials and designs to prevent overheating. This includes considering the wire's diameter and the insulation's thermal properties to ensure they are suited for the motor's operating conditions.
Implementing a Comprehensive Motor Maintenance Plan
A proactive approach to motor maintenance is your solution to prevent overheating and ensuring the electric motor's longevity. An effective maintenance plan encompasses early detection and correction of potential issues that could lead to overheating.
Regular inspections, performance monitoring, and timely repairs are essential components of a comprehensive maintenance strategy. This proactive approach helps identify issues like misalignment, bearing failure, or lubrication problems before they lead to overheating.
For more tips on how to handle complex equipment or machinery, check out our complete guide to machine safety.
Find High-Quality Electric Motors from Trusted Suppliers at RS Philippines
If you’re looking for electric motors for a wide range of applications, you can find them at RS Philippines. Browse through our catalog of AC motors and DC motors to find the right one for your needs. Rest assured that we only source components and equipment from trusted suppliers worldwide.
Recommended Brands for Electric Motors
Omron
Renowned for their high-quality AC motors, Omron provides you with electric motors for reliability and efficiency in various industrial applications. Omron’s AC motors are equipped with innovative features to ensure optimal control and energy savings, making them ideal for automation systems.
Crouzet
Crouzet stands out in the electric motor industry by offering a comprehensive range of both AC and DC motors, catering to a wide array of applications. The brand's dedication to quality and innovation is reflected in the durability and performance of their motors, which are designed to meet the rigorous demands of industrial use.