- Published Feb 21, 2024
- Last Modified Apr 4, 2024
- 9 min
Decoding Material Handling: Manual vs. Automated Approaches Unveiled
Explore the world of material handling – from manual to automated approaches. Make informed choices for efficient, safe, and scalable operations with RS.

Material handling, an essential component of modern industrial and commercial operations, is experiencing significant growth, particularly in the Asia-Pacific region.
As a matter of fact, according to Data Bridge Market Research, the material handling equipment market in this region is poised to reach an impressive EUR 35,931.80 million by 2030. How is that possible, you ask?
As a vital component of supply chains, warehouses, and distribution centers, the material handling equipment market is instrumental in ensuring the smooth movement and management of goods. Moreover, with the global economy expanding, the demand for efficient, safe, and reliable material handling solutions is also surging. This is complemented by heightened safety concerns, especially since the manufacturing sector in the Philippines reports the highest incidence of workplace injuries compared to other industries in the country. Additionally, the escalating need for lifting operations in ports further fuels this market's expansion. All of the aforementioned play a role in further driving the growth of the material handling equipment market.
But what exactly is material handling equipment? This question sets the stage for understanding the critical role these tools play in modern business operations and the evolving dynamic between manual and automated approaches in this field.
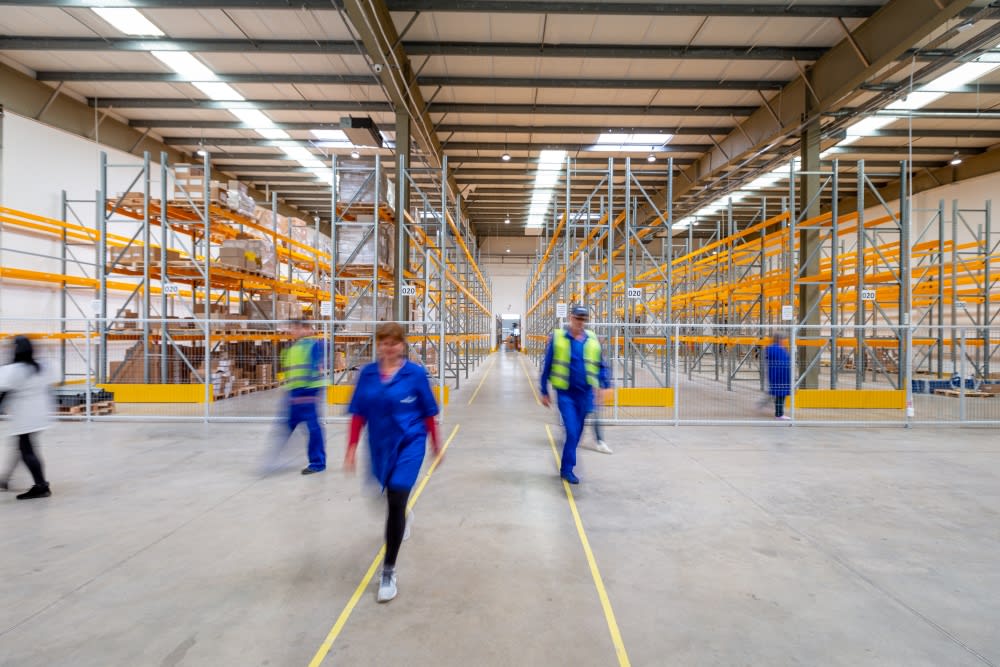
What is Material Handling?
Material handling forms the backbone of operations in many large corporations. It encompasses the crucial processes of moving, protecting, storing, and controlling materials, work-in-progress items, and finished goods within a facility. This process is integral not just for maintaining the flow of operations but also for ensuring safety and success in various sectors, including manufacturing, production lines, warehousing, and distribution.
How Many Types of Material Handling Are There?
There are essentially two types of material handling: manual and automated.
Manual handling involves physical labor and simple tools, while automated handling, also known as AMH, involves semi-automated or computerized material handling equipment or any other machines that leverage technology like (AI), the Internet of Things (IoT), and robotics to streamline operations.
What is Material Handling Equipment?
Material handling equipment refers to the tools and machines used for handling various materials in industrial and commercial settings. This equipment ranges from basic devices like pallet jacks used in manual handling to more complex systems like conveyor belts, automated storage and retrieval systems, and intelligent robotics used in automated processes.
Understanding Manual Material Handling
As mentioned, manual material handling is a process where workers physically manage and move materials using their strength and skills. Be it through the use of hand trucks in retail stores for moving stock or pushing building materials up ramps at a site; this method primarily involves various actions that often necessitate significant human effort and interaction.
Due to the heavy reliance on human labor, manual material handling is deemed to be highly adaptable and flexible for different tasks and environments. It also allows for precise control and is often used in situations where handling delicate or irregularly shaped items is necessary. Moreover, manual material handling is particularly prevalent in smaller operations or environments where automation is not feasible due to space constraints or the nature of the tasks.
At the same time, manual material handling comes with its set of limitations, too. For one, it can be physically demanding and poses a risk of injuries, especially musculoskeletal disorders, due to repetitive strain or improper lifting techniques. The efficiency and speed of manual handling are also generally lower compared to automated systems, making it less suitable for large-scale or high-volume operations.
Embracing Automation in Material Handling
However, the simultaneous evolution of technology in material handling marks a significant shift from manual methods to automated systems.
With rapid advancements in robotics, machine programming, and sensory technology, there's a growing trend toward full automation in material handling. This shift is not just about replacing human labor but also about enhancing efficiency, accuracy, and safety in operations. As such, it comes as no surprise that AMH systems, integrated with AI, IoT, and advanced robotics, are transforming the landscape. After all, they are enabling smarter, data-driven decision-making and opening up new possibilities for optimizing material handling processes.
Presently, a considerable portion of material handling machinery is semi-automated, still requiring human intervention for tasks such as driving, loading, and unloading containers. And the benefits of such shifts extend beyond mere efficiency gains; they also significantly reduce the physical strain on workers and streamline operations in diverse industrial settings.
Overview: Key Differences Between Manual and Automated Approaches
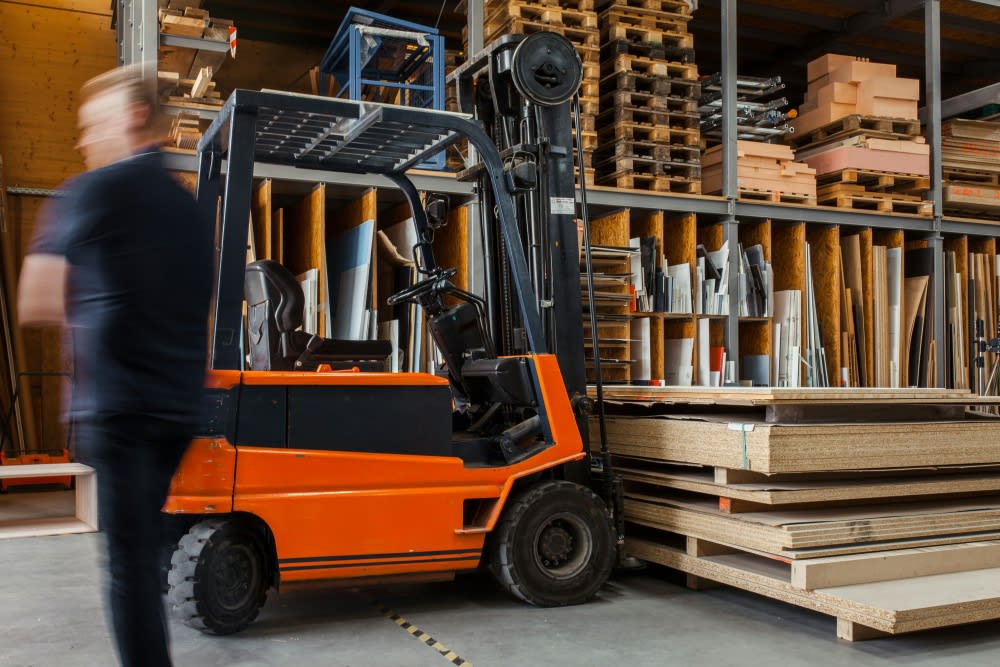
The distinction between manual and automated material handling is pronounced, primarily in terms of labor, cost, and adaptability. Consider the following differences:
|<br>Aspect<br>|<br>Manual Material Handling<br>|<br>Automated Material Handling<br>| |-|-|-| |<br>Labor Intensity<br>|<br>High, relies on physical human effort.<br>|<br>Low, relies on machines and technology.<br>| |<br>Cost<br>|<br>Lower initial costs but potentially higher long-term expenses due to labor and injury-related costs.<br>|<br>While it may require a greater upfront investment, this approach can result in long-term cost reductions by decreasing labor expenses and improving overall efficiency.<br>| |<br>Adaptability<br>|<br>Highly adaptable to various tasks and environments. Can handle irregular and delicate items effectively.<br>|<br>Less adaptable, typically designed for specific, repetitive tasks. May struggle with irregular items.<br>| |<br>Efficiency<br>|<br>Can be less efficient for large-scale operations due to reliance on human speed and endurance.<br>|<br>Generally more efficient, especially in high-volume or repetitive tasks, due to consistent machine operation.<br>| |<br>Risk of Injury<br>|<br>Higher risk of musculoskeletal and other injuries due to physical strain.<br>|<br>Reduced physical strain on workers, potentially lower risk of injury.<br>| |<br>Operational Speed<br>|<br>Depends on the skill and endurance of the workforce. Can be slower in large-scale operations.<br>|<br>Consistently high operational speed, not affected by human limitations.<br>|
Factors Influencing the Choice: When to Go Manual, When to Go Automated
Deciding between manual and automated material handling involves evaluating various factors to determine the most effective approach for a specific operation.
Consider the following:
- Type of Materials: Manual handling is often more suitable for delicate or irregularly shaped items requiring careful handling. Automated systems are ideal for standardized, repetitive items.
- Operational Volume: For high-volume operations, automated handling can significantly enhance efficiency and throughput. Manual handling is more feasible for lower volumes or variable demands.
- Cost and Return on Investment: While manual handling has lower initial costs, automated systems can offer long-term savings through labor reduction and increased efficiency. An ROI analysis is crucial to assess the financial viability of automation.
- Safety and Ergonomics: Manual handling poses a higher risk of physical injuries due to strain and repetitive motions. Automated systems typically provide safer environments by reducing the physical demands on workers, although they require rigorous safety protocols to prevent accidents involving machinery.
- Space and Infrastructure: Automated systems often require significant space and infrastructure changes. Manual handling is more flexible and can be implemented in restricted or existing spaces without major alterations.
- Flexibility and Adaptability: Manual handling offers greater adaptability to changing processes or products. Automated systems are less flexible but are highly efficient for consistent, repetitive tasks.
- Worker Skill and Training: Manual handling relies on skilled labor and training, particularly for safe and ergonomic practices. Automated systems demand technical expertise for operation and maintenance.
- Technology Integration: Automated handling allows for better integration with advanced technologies like AI and IoT for data-driven operations. Manual handling is less conducive to such integration.
Assessing these variables enables enterprises to make well-informed choices, striking a balance between effectiveness, expenses, security, and adaptability to select the most suitable material handling strategy tailored to their particular requirements.
Future Trends in Material Handling
The material handling industry is rapidly evolving, with several future trends poised to reshape its landscape:
- Emerging Technologies: Advanced technologies like AI, IoT, and robotics are increasingly being integrated into material handling. This integration is enhancing the efficiency and intelligence of automated systems, allowing for more responsive and adaptable operations.
- Sustainability Considerations: There is a growing emphasis on eco-friendly practices within material handling. This includes the development of energy-efficient machinery and the implementation of practices that reduce the environmental impact of material handling operations.
- Adaptation to Evolving Business Needs: The material handling industry is adapting to the changing needs of businesses, such as the demand for more flexible and scalable solutions. This includes smarter and more complex equipment that can evolve with a company’s changing requirements, ensuring long-term viability and effectiveness.
Navigate the Future of Material Handling with RS
As the material handling industry continues to evolve with emerging technologies and sustainability trends and efforts, RS Philippines stands at the forefront, ready to guide and support businesses through these dynamic changes.
At RS, we recognize the importance of staying ahead in this rapidly transforming field and offer a diverse range of the proper material handling equipment that caters to both current and future demands. From crane lifting equipment to moving equipment and accessories, we offer a comprehensive range of solutions to meet your material handling needs.
Partner with RS to equip your business with advanced material handling equipment that is designed to meet the challenges of today and adapt to the opportunities of tomorrow.
Popular Material Handling Equipment Brands
Related links
- Telemecanique Sensors Application material handling Series
- Ansell HyFlex 11-618 Blue Nylon General Handling Size 9,...
- Liscombe 421 Grey Leather General Handling Size 8
- Liscombe 421 Grey Leather General Handling Size 12
- Liscombe 421 Grey Leather General Handling Size 11
- Liscombe 421 Grey Leather General Handling Size 10
- Liscombe 421 Grey Leather General Handling Size 9
- Liscombe 414 Yellow Leather Material Handling Work Gloves, Size 9